Editor's Pick
Safety first
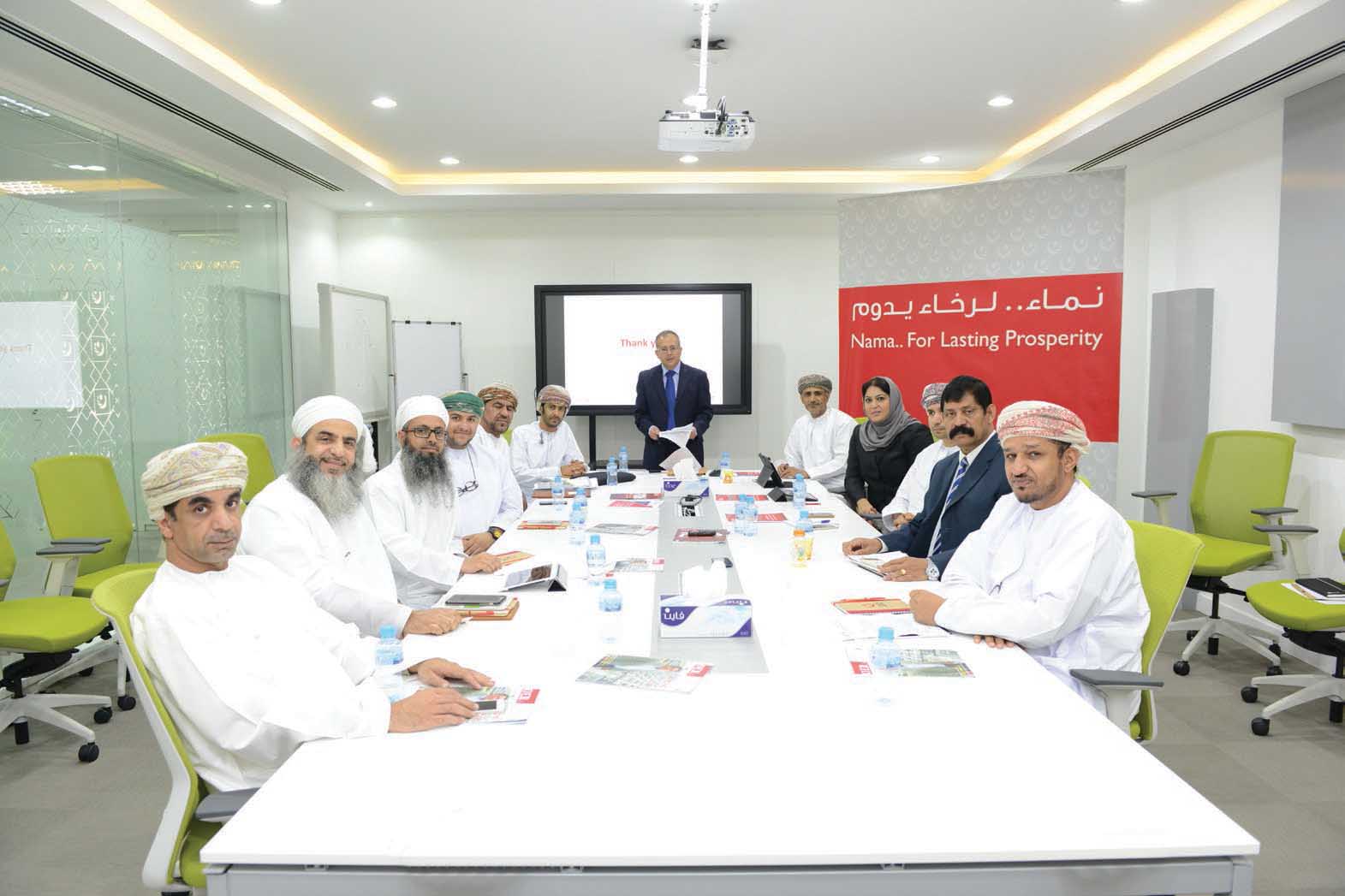
A roundtable discussion on Health Safety and Environment (HSE) organised by the Nama Group and OER calls for a regulator or an authority to implement HSE regulations and sharing of best practices between companies
Moderator: Welcome, everyone. Initially, we want to get your thoughts on HSE practices in the country. I would like to start with Younis, because PDO and the oil and gas sector have always had strict norms about HSE. What are your thoughts about it?
Younis Al Hinai: If I talk about HSE practices within the country, there is no single entity that takes care of it. Every governmental body is allowed to issue its own requirements and specifications. I am sure if you ask all the attendees here if they fully comply with HSE rules and regulations in Oman, no one can say yes, because they don’t know them all. We don’t have a single point of reference. Every single government body, whether it be the Ministry of Manpower, Ministry of Health, Ministry of Legal Affairs, Ministry of Regional Municipalities and so on have their own HSE standards and requirements. We have historical HSE rules and regulations but we don’t know about them. So we cannot say we are complying with it. In PDO, we are currently undertaking a project to bring together all HSE-related Royal Decrees, ministerial decision and local orders to look into how we can comply with them. So it is a very wide and diverse topic.
Moderator: Salim, you had worked with ORPIC and now you are working in the aviation sector. Younis has raised a very important point that there is no nodal agency to regulate HSE in the country. What are your thoughts on it?
Salim Al Harthy: Aviation is a much regulated business. We have to strictly abide by the rules and regulations. What I understand from the presentation here is that we don’t have a benchmark. In UK, for example, all the companies need to abide by certain standards, set by an approved company or authority. I would like the idea of the license being issued from one company or regulating authority. Only a regulator can issue the license. We should have a standard that all companies should comply with. It is not all about complying with ISO standards only, because ISO is all about documentation. There is no enforcement.
Moderator: What’s your take Eng. Ali on the issue?
Eng. Ali Shamas: I think ours is a regulated business. Especially in electricity, we have a regulator. We have 46 HSE requirements which we consider as a legal requirement to comply with in the sector. But in certain other sectors, you need to have certain requirements specific to that particular sector and when new situations emerge we need to address it. But in the electricity sector, to a certain extent we have certain fixed HSE requirements as we don’t have new things coming every day. There is space for a regulator in the electricity sector either in the capacity of an advisor or an authority.
Moderator: Prabhakaran, you represent engineering and construction sector which employs a lot of people. How are HSE standards in the sector?
K C Prabhakaran: We are basically a service provider for PDO and for the Ministry. The HSE practices we follow are mostly taken from PDO which has got a very good system with respect to managing HSE. Those things are being replicated for our non-PDO jobs and that are well accepted by all our major clients. We have done the tower line from here to Mudhaibi to Al Kamil for which we have used a PDO system. We have completed it without any LTI and without any accidents. So the system what I am aware of is the PDO system which is very well controlled by PDO.
Moderator: Abdullah. What are your thoughts on HSE practices at the government level?
Abdullah Al Balushi: We have a very good systems in place and we are implementing it very well.
Moderator: Eng. Abdullah, do you want to add something to that?
Abdullah Al Busaidi: I think in Oman we should adhere to PDO’s HSE practices because they are the best in the industry.
Moderator: Musallam, you have recently joined Nama group as HSE manager. What’s your plan to enhance HSE practices within the group?
Musallam Al Khaifi: I have not completed my first month yet. But I am doing all the diagnostics. I have already promised to the executives that I am going to present them my vision. But the system we have in the company is very rigorous and tough. But we have to make sure that everybody, especially our contractors, comply with the system. The second thing is that if you don’t believe that you need HSE, then it’s very difficult to make you comply with it. I remember my grandfather did not want to go to hospital or take medicines because he did not think that he was sick, even though he was not well. I agree with what Younis and Salim said that we need an overall regulator or an authority to implement the system.
Moderator: What are the causes of accidents and fatalities in your respective sectors and what are the preventive measures to stop them?
Salim Al Harthy: Changing people’s mindset and building a new culture is very difficult. The only way to enforce HSE is constant training, benchmarking and creating a culture especially among the contractors.
K C Prabhakaran: We built around 50 per cent of the power projects in Oman and we have a very good track record. I am saying this in my capacity as working in Oman for the past 24 years which includes two years with PDO and 22 years with Al Hassan.
Moderator: Eng Ali, where are you, in terms of training, benchmarking and creating a culture of compliance?
Eng. Ali Shamas: Building culture is very important and that is where we have to put a lot of energy. We need to work a lot with small and medium companies in the electricity sector. First, we need to make sure that we have very rigorous compliance requirements. That should be the first priority. Second thing is that they should have all electrical members. We check them two times. Once the contract is given to them, we have to track them at key areas like cable cutting. If they violate we have to stop them from bidding for the next time or penalise them. In addition, now we have started an initiative to train and teach our heavy equipment vehicle drivers and excavators and we issue a license to them.
K C Prabhakaran: Training is very important because people are coming from different countries and they don’t have previous experience in handling the new jobs. Distribution Code Review Panel (DCRP) is one of the regulatory bodies which issues license to the people. These are the two areas we have to improve. Contractors are not wilfully committing any wrong. We have trained and developed many people. Contractors can do a lot because they are the executors. They need to implement the rules and regulation laid down by you. It should be in a booklet format and should be translated for trainees. This will enhance their knowledge and enable them to do their job without any problem. PDO is still having LTIs, but those LTIs compared to the quantum of work that they are executing, is negligible, because they have a system of mandatory training. A person coming from India never knows what the safety issues are here in Oman. Therefore you need to educate them; if you don’t educate them and ask them to do the job, they will end up meeting accidents. PDO has done a lot in this respect which can be emulated in the electricity sector as well, so we can definitely do much better.
Eng. Ali Shamas: I can vouch for that. When I was in PDO we started a novelty health club. We used to have even Bedouins. We used to interview them and train them well. Safety involves three things. First comes awareness. Second thing is behaviour i.e. compliance to rules and regulations. Then comes what we call concentration. These are the ABCs of safety.
Salim Al Harthy: I may add something to complement what he said. We don’t like too much birds in the airport. If they strike the aircraft and get inside the engine, then an engine will fail. We found that some people working in a cleaning company used to bring food in their pockets and feed the birds in the runaway, because they believed feeding birds will bring divine blessings. We approached them and spoke to them in their language. We asked them if saving 200 people’s lives is more important than saving one person’s life. They replied in affirmative. Then we told them God will love you more if you save 200 people than saving one person. We need to speak to them in their own language.
Musallam Al Khaifi: We keep on talking about PDO. PDO is 45 years old. I worked in PDO for 17 years. PDO adopted the standards of Shell which is a 200-year old company. It has journeyed to this level of perfection and excellence. No matter how many standards, policies and procedures you create, no company can embed HSE into their functioning culture within a short span of time. But that takes time. We adopted a lot of standards from PDO just like PDO adopted from Shell. There was no lifesaving rules in PDO till 2007 when it was first introduced by British Gas. Then PDO adopted it.
Moderator: Can you talk about something tangible that you can do to improve the situation in the company during the next six months?
Musallam Al Khaifi: First, I will try to find out what is lacking. I already have the audits of what we have done in the company. I will identify the areas where we are lacking. We have very nice programmes here, but we cannot achieve some of them in such a short period of time. For example, behaviour- based tools cannot be implemented in six months. The minimum time you need to embed them in 200 people is two years. We have a very good programme to improve HSE and most of them are very straightforward such as creating lifesaving rule, whereas there are some plans which we need to review. My vision is to make Nama one of the leading HSE company’s in Oman and in the region.
Moderator: Is it unrealistic?
Eng. Ali Shamas: As Musallam said we are very optimistic. Everything cannot be done in one day. We have a lot of things to do. When I came to Dhofar Power, I found a problem between my operation manager and my HSE manager. When something happened, the operation engineer said the HSE manager is responsible for that. I told him, “No. You’re responsible about everybody’s safety.” Even I am, as a CEO, responsible to ensure safety. We need to implement the culture from top to bottom.
Musallam Al Khaifi: It’s all about what kind of behaviour you need to encourage and what kind of behaviour you need to get rid of. Then you need to come up with a plan to build your environmental system. Then you have to train your people – 2,828 people plus the contractors. Then you have to implement it and for implementing you need a system.
Moderator: But here the issue is the time-frame.
K C Prabhakaran: You are talking about 2,828 people that you have to cover within six months. That is impossible. You can cover these many people within six months, provided you identify certain people from the contracting community and train them whereby these people impart and cascade the subject down to other people working in their respective companies. But for getting results, it will take at least a minimum of one year.
Salim Al Harthy: Nothing would be possible without commitment from the top. If everybody from top to bottom does not talk the same language, nothing will happen. If you go and preach something and do something else, none would trust you.
Eng. Ali Shamas: You touched exactly what I am heading for. In the first six months, we need to see the areas where we need to do some fixing. We should look at the areas, where there are more accidents happening. Of course, in order to have a behaviour system or culture in place, we have a long way to go. You have 2,800 plus Nama Group employees plus contractors and that is a huge number. For us in Dhofar Power, it took us three years to implement a small safety culture programme. We first started with our staff and then moved to our contractors.
So what we are looking to do in the next six months is to contain certain repetitive accident patterns that we have at Nama group. But we can embed the behavioural system only in the long run.
KC Prabhakaran: What I want to talk about is BBS. In BBS, we should not focus on electrical jobs alone, because BBS has got different areas of interest. In PDO, they have started some two to three years back, IVMS implementation. Initially, there were a lot of variation. But today we have reached a stage where we are able to control the behaviour of our drivers and reduce accidents drastically.
Abdullah Al Busaidi: I would like to stress on culture and education. Sadly no one asks about employee education. Most of the employees have minimum certificate qualification from India and other places. A majority of them are unaware about work and safety norms. That’s the reason why many accidents happen on site. It is pertinent to consider about safety cost. If the tender amount is RO20,000, what is the safety cost? How do I spend for HSE if the cost of the tender comes down? I simply can’t. HSE comes at a cost. We have to ponder over safety cost.
Moderator: Dr Ali Shamas, there are budgetary constraints that the country is facing. How do we strike a balance between maintaining HSE and budgetary constraints?
Eng. Ali Shamas: Safety certainly comes at a cost. And it has to be improved step by step in order to create a safety culture. We need to work together as to how to minimise the cost and also utilise our resources. Now we are utilising the staff as trainers, so that costs are reduced. Whenever needed, we have invited companies from outside, which are specialised firms. So we have agreed with them on the cost per person.
K C Prabhakaran: Wherever possible, it is necessary to bifurcate the contractual and safety amount separately. Safety amount should be incorporated in the bid. Most of the contractors try to reduce the requirement and they want to make that money as profit. If that can be bifurcated in the contracted bid, then it can be a good solution.
Moderator: Anything else that needs to be done?
Eng. Ali Shamas: We need to work together if we want to improve safety. We also need to work on standards. We know that contractors is one of the areas to work on. We now have corporate audit for all the companies.
Salim Al Harthy: It’s good to be done by the companies. However, a minimum standard needs to be maintained.
Musallam Al Khaifi: We already have best practices in place in our subsidiaries. I see no reason why companies can’t share best practices. We can share knowledge. Reducing HSE training or postponing training is not the solution in the era of oil price decline. And earnest efforts should be made to reduce the cost.
K C Prabhakaran: Today non accidental deaths (NAD) are increasing. In a month or two, I have seen five to six NADs. The focus should not be on safety alone, but the health aspect should also be included.
Abdullah Al Balushi: HSE incidences and procedures need to be shared
with all.
Moderator: What can others learn from PDO’s experience?
Younis Al Harthy: HSE includes health, safety and environment. We need to look into all three aspects, not just safety. As far as language is concerned, PDO has so many different nationalities. There is need for training and methodology of training. We conducted an audit in 2014 on our HSE training standards. We have revised all our training modules. If you see there are 600 pictorial slides now without any word. We have gone visual and made it very simple, easier to understand. There is a much deeper engagement in the training class. Now, we facilitate discussions within the training class. This is a big step forward in our training approach. In addition, there is competency assessment after training. The other aspect is simplicity. In PDO, we have so many procedures. If you look at our HSE documents, there are more than 220 procedures of specifications. Now we are simplifying all the requirements. For a worker in the frontline, he can have all the safety aspects on a single page. Additionally, we are reviewing the HSE recommendations to enable people to comply. Lifesaving rules have been simplified. We have made sure people understand it easily. Yet another aspect is engagement – from top management to the lower rung. We have also introduced a simple tool on reporting near misses. Near misses are very powerful incidents that could lead to injuries and fatalities. Currently, the PDO staff and other contractors can log onto our website and report near misses. If we come to know of near misses, we take measures to prevent them.
Moderator: How has the introduction of Health and Safety Management systems like OHSAS 18001 improved safety performance?
Salim Al Harthy: Compliance and certification can be effective if it is not done just five days or a week before the audit. If it is not practiced, continuously and on the ground level, then it is not of any use. People should know that a certification is not good just for the sake of certification, but it has to be practiced.
K C Prabhakaran: We are OHSAS 18001 certified, so what happens is that one is always prepared, for the external audit. There is an audit plan, so it is not once in a year exercise. When you work with PDO, every week there is an audit, and that helps.
Musallam Al Khaifi: I have seen these certificates becoming mere framed papers on the wall, telling people we are there. These certifications are a good tool if action is taken on them and they are not used merely for enhancing ones reputation.
Eng. Ali Shamas: These international certifications are guidelines, there are some companies which may not have these certifications but they are very good and some of the companies which have them may become complacent. There is a documentation part to safety and these certifications help in it. They also help in continuous improvement, there is no question that there is an added value. Yet at the end of the day, the target of all HSE measures is to save life, if a certification helps in saving – life, environment and health then without doubt it is positive for the company. If despite doing all these a company is not improving then it means that you already had a good procedure, and the certification has not added value to what you already had.
Moderator: There is a perception that not all accidents and near misses are being reported and we are losing the opportunity to learn from these? What needs to happen to improve incident reporting?
Younis Al Hinai: There is no clarity on what defines a near miss, so it is important to understand as to what defines a near miss. At PDO, we have tried to simplify things. Helping people to report on near misses in the past was very difficult, as there was a feeling that the management may come down heavily saying -how did this happen? So people felt a bit reluctant to report. We devised a tool, so we now have a small manual stating – What happened? When did it happen and why did it happen? It is an anonymous system and one does not even need to report ones name. This has helped in increasing the reporting of near misses. As a part of this package, we had a short video which narrates what was a near miss, safe act and a safe condition. We have looked into the loss prevention pyramid, as this includes fatalities, major injuries, near miss, unsafe acts and unsafe conditions. This has helped in raising awareness within the organisation.
Moderator: Fatalities and serious injuries from road accidents continue to occur each year. Research has shown for the utilities sector internationally, this is one of the most frequent causes of accidents. What improvements can be made in this area?
Eng. Ali Shamas: In the electricity sector the mileage clocked is not the same as some other sectors, but we are learning from other companies like PDO and implementing things like defensive driving and are working on this with our contractors.
Younis Al Hinai: At PDO we look at road safety from three perspectives – one is the driver, the second is the vehicle and the third is journey management. For the driver we have a tracking system, the vehicle has to meet certain specifications. Now we have combined journey management with IVMS (Integrated Vehicle management system). We are tracking thousands of vehicles within PDO and its contractors. At PDO we have not had an LTI for the last two to three years.
Salim Al Harthy: IVMS and awareness helps in reducing the incidents of accidents. We have introduced a new system wherein a person who speeds over a certain limit is warned or even stopped from driving.
-
OER Magazines1 month ago
OER, July 25
-
Alamaliktistaad Magazines1 month ago
Al-Iktisaad, July 25
-
Education2 months ago
Russia offers diverse tourism and education opportunities: Sofia Malyavina
-
Digital2 months ago
Russia’s Digital Frontier: An Inside Look with Alexey Goreslavsky of IRI
-
News1 month ago
OpenAI Strengthens ChatGPT’s Mental Health Safeguards Ahead of GPT-5 Launch
-
Banking & Finance2 months ago
Sohar International Partners as Main Sponsor for Refill 3, a Culinary and Cultural Festival Driving Tourism in Khareef Dhofar
-
Banking & Finance2 months ago
Tender results of Government Treasury Bills worth RO21.7 million issued
-
Energy2 months ago
Oman Investment Authority launches the Sultanate’s First Energy Transition Fund
You must be logged in to post a comment Login