Experts
Technology, Innovation and Collaboration Drive Produced Water Strategy
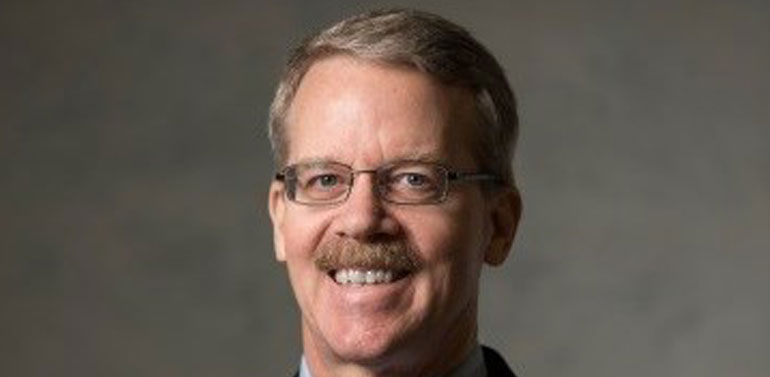
Technology Evolution
Produced water can be treated through gravity separation, flotation, and filtration to physically or mechanically remove contaminants. Various proprietary technologies are employed, with their application dependent on the nature and volumes of the fluids being produced, asset type and location, and environmental legislation.
The first stage of the separation process relies on the effects of gravity and density difference, whilst the fluids remain within the separator. Here, a long residence time, relative to the differential specific gravity of the phases is essential. The simplest solution is to employ a large tank for storing the produced water where time facilitates the separation, rather than any advanced technology-driven process within the tank itself.
Offshore, the requirement for a long residence time must be balanced against the footprint (size and weight) limitations placed on the separation tank. Several technologies are employed to eliminate oil droplets at the primary separation (gravity) stage, including hydrocyclones and plate coalescers. This is followed by flotation and filtration, with adsorbents and absorbents typically used after the tertiary (filtration) stage. Adsorbents and absorbents have seen development of innovative media solutions combining the two mechanisms of removal.
Offshore technology evolution has been driven both by regulation and by project economics. With floating production, storage and offtake facilities being billion-dollar propositions, there is huge benefit to reducing the weight of produced water solutions while ensuring high reliability to remove the need for redundancy, both of which translate to a smaller footprint.
Having met local mandates, there are producers in Norway that are now looking to exploit technology advancements to recover more crude. The CTour process is one such example. Based on extraction principals, it is one of the only technologies in the world that can cost-effectively remove both dispersed and dissolved hydrocarbons from large volumes of produced water, while effectively increasing the crude that can be recovered. Whereas the best available technology for de-oiling produced water is a hydrocyclone/degasser-float cell configuration that yields an average discharge concentration of less than 25 ppm oil and gas, the CTour process can yield a residual oil discharge as low as 2-3 ppm TPH while removing 90-95 per cent of hazardous dissolved hydrocarbons.
Named in honour of the French scientist Cagniard de la Tour, who first discovered the phenomena of super critical fluids in 1822, the CTour process can treat large volumes of produced water at low weight, height, footprint, and capex and opex, while reducing overall chemical use. This represents a shift in produced water management, and future legislation based on this technology is anticipated.
A Strategic Concern
Certainly, there are several produced water technologies available today that are much better than the technology currently employed on some platforms. But with cost and compliance being primary factors dictating solution choice and dependent on whether you are talking to an E&P or engineering, procurement and construction (EPC) company, adoption of more innovative technologies will often be gradual.
Yet the fact is that technology choices made at the project outset can heavily influence long-term opex, and thus an asset’s overall profitability. For new builds, where produced water volumes will not be significant in the first few years of operation, there is a certain level of deduction necessary when it comes to assessing the technology requirement, which is where the experience of a produced water specialist can come to the fore in terms of reducing the potential cost of a retrofit later on versus installation from the start.
Likewise, if the operator intends to either decommission an existing asset or sell it on in the short-to-medium term, they may be unwilling to invest in a more expensive solution. However, selecting a lower cost solution purely because it does the job and meets the regulatory mandate can be risky. Issues can be encountered as produced water volumes rise, or should the chemistry of the reservoir change over time, so a capex-driven decision at the outset can prove false economy.
Historically, EPCs, and in some cases producers, have sought the lowest cost option whilst ensuring they are not exposed to long-term liability issues. However, analysts at IHS have warned that water management risks have increased rapidly in the past six years, due to regulatory compliance requirements, costs, concerns over water scarcity and quality, and the industry’s need to preserve its social license to produce the hydrocarbons.
-
Banking & Finance2 months ago
Oman Arab Bank Announces Increase of Authorised Capital to RO500mn and Paid‑In Capital Boost of RO50mn
-
Bahrain2 months ago
SPIEF 2025 focused on global and regional economic processes, market transformation, new tech, investment climate, financial policy and people
-
Banking & Finance1 month ago
National Finance Reinforces Position as Partner for Growth, Offers a Comprehensive Product Suite to Support Customer Ambitions
-
OER Magazines2 months ago
OER, June 25
-
Energy2 months ago
Russian Energy Week from October 15-17, 2025 offers alternative formats of cooperation
-
Alamaliktistaad Magazines2 months ago
Al-Iktisaad, June 25
-
Technology2 months ago
SPIEF 2025 showcases cutting-edge technologies and digital innovation through its Innovation Space initiative
-
Energy2 months ago
The year 2025 is a special year for Oman and Russia as it marks 40 years of diplomatic relations between the two countries says HE Sergey Tsivilyov, Energy Minister of Russia
You must be logged in to post a comment Login