Experts
Technology, Innovation and Collaboration Drive Produced Water Strategy
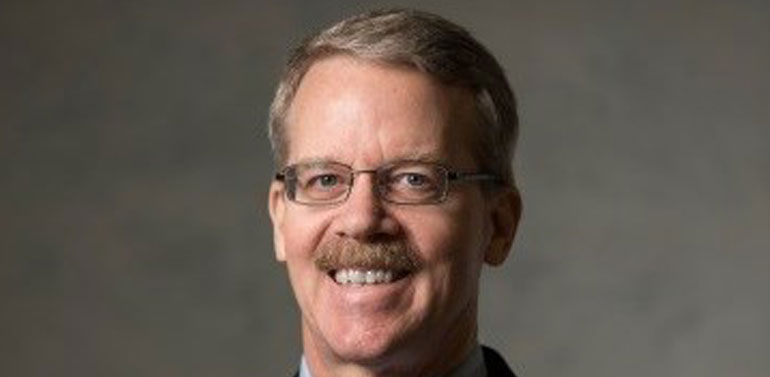
The aging of conventional wells and the boom in shale development have sparked a sharp increase in the volume of water produced by oil and gas production. Horizontal drilling and water-based hydraulic fracturing programmes onshore are far more water-intensive, while water cuts can be as high as 80-90 per cent in wells in aged, depleted reservoirs.The focus on produced water issues has grown in prominence not only because of the rising volumes of water generated by oil and gas operations, but because the industry is increasingly risk-averse and environmentally-aware.
In Norway, there are producers looking to reduce the amount of oil in water (OiW) to as close to zero as possible, as regulators and environmental agencies begin to monitor soluble components in addition to the free and dispersed oils (the small droplets of oil suspended in the produced water).In the UK North Sea, the current performance standard for dispersed oil in produced water is set at 30 parts per million (ppm). In the US, the effluent limitations guidelines (ELGs) enforce limits of 29 ppm for offshore wells and impose a zero-discharge requirement for produced water onshore. Meeting such performance standards has become more challenging for exploration and production (E&P) firms as water production increases.
E&P firms need strategic partners with the ability to provide proprietary technology, global project management and rapid response to address their specific produced water challenges and optimise operations and returns, writes ProSep’s CTO, John B. Sabey
Growing Market
Produced water can come from both conventional and unconventional wells. Typically, it contains a combination of hydrocarbons and other constituents. These include salts, chemical additives and toxic compounds, as well as solid wastes with harmful substances such as boron, sulphates, radioactive elements and heavy metals.
The water already present in the reservoir (formation water) and the use of water injection techniques to aid the secondary recovery process (EOR – enhanced oil recovery) generates by far the largest volume by-product stream, with some 21 billion barrels (bbl) of produced water generated each year in the US alone. With 1 bbl equating to 42 gallons, this figure represents about 57 million bbl – or 2.4 billion gallons – per day, according to the US National Energy Technology Laboratory (NETL).
The growing volumes of produced water have meant E&P firms have effectively become water management firms. They are spending an increasing amount of time, effort and resources treating water for use and re-use, reinjection or environmentally acceptable discharge. NETL puts the water-to-oil ratio – i.e. the volume of water produced for every barrel of oil recovered – at between 5:1 and 8:1 in the US, and between 2:1 and 3:1 worldwide. Meanwhile, analysts at BCC Research believe that the water-to-oil ratio in North America will increase to 12:1 over the next 12 years – and 50:1 in the worst cases. With producers paying anywhere between $3 and $12 per barrel to dispose of produced water, the research firm expects the North American market for produced water treatment equipment to reach $1.2 billion by 2017.
Case By Case Solution
The physical and chemical properties of produced water vary considerably depending on the geographic location of the field, the geologic formation, and the type of hydrocarbon product being produced. It is typically comprised of certain amounts of oil and solids, and a specific droplet size distribution.The produced water will also have a specific chemistry, dependent on the chemical characteristics of the formation and the hydrocarbon. It may also include water from the reservoir, water previously injected into the formation, and any chemicals added during the production processes. Moreover, all of these properties and the produced water volume will vary throughout the lifetime of a reservoir.
As such, produced water is unique to every asset. Indeed, there could be two wells that are two miles apart and within the same formation that have totally different chemistries, oil, solids and droplet sizes. There could even be different produced waters coming into the same platform from two different wells, and it is not uncommon for these chemistries to mix together and compound processing issues such as scaling.
The water treatment and filtration requirements of upstream installations are therefore myriad and diverse. It is the characterisation and composition of the produced water that dictates the types of treatment technologies necessary to meet mandated limits. Flow rate dictates the size and quantity of the equipment needed, while the final specification and design is also dependent on how the asset operates currently, what condition it is in, production method and location. The most important consideration is the final destination/use of the produced water.
-
Banking & Finance2 months ago
Oman Arab Bank Announces Increase of Authorised Capital to RO500mn and Paid‑In Capital Boost of RO50mn
-
Bahrain2 months ago
SPIEF 2025 focused on global and regional economic processes, market transformation, new tech, investment climate, financial policy and people
-
Banking & Finance1 month ago
National Finance Reinforces Position as Partner for Growth, Offers a Comprehensive Product Suite to Support Customer Ambitions
-
OER Magazines2 months ago
OER, June 25
-
Energy2 months ago
Russian Energy Week from October 15-17, 2025 offers alternative formats of cooperation
-
Alamaliktistaad Magazines2 months ago
Al-Iktisaad, June 25
-
Technology2 months ago
SPIEF 2025 showcases cutting-edge technologies and digital innovation through its Innovation Space initiative
-
Energy2 months ago
The year 2025 is a special year for Oman and Russia as it marks 40 years of diplomatic relations between the two countries says HE Sergey Tsivilyov, Energy Minister of Russia
You must be logged in to post a comment Login